Valve actuators are mechanical devices that open and close valves to allow or stop the flow of a fluid through a system. They are available in many variations, each of which offers different advantages and disadvantages that make it suitable for distinct applications. Two of the most commonly used types are pneumatic actuators and electric actuators. Pneumatic actuators utilize compressed air to operate valves, while electric actuators use an electric motor. Below, we go more in-depth on the differences between the two to help readers choose the best one for their application.
How Do Electric Valve Actuators Work?
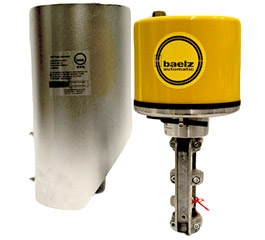
Electric actuators work by generating a linear force through the conversion of rotational force, often through the use of ball screws or other methods. When the actuator's screw rotates along with the motor, the actuator's ball screw nut travels forward or backward along the screw.
The regulation of electrical currents and voltage determines the position of the actuator.
How Do Electric Valve Actuators Work?
What makes electric valve actuators different from other types of valve actuators is their ability to open, shut, or adjust valves through the conversion of electricity in a rotary or linear motion.
The movement you want to control will depend on the actuator design. For instance, rotary electric valve actuators could operate using one of the following methods that rotates up to 90 degrees to open and close the valve:
- A butterfly valve
- A plug valve
- A ball valve
In addition to the type of motion you want, another key consideration when selecting an electric actuator valve is the specific voltage. The voltage of the valve should match that of your facility's existing electrical systems. For instance, you might have a facility with power sources that use either direct current (DC) or alternating current (AC).
Rotary valves must also generate torque, which is the rotational force that allows operators to open and close the valve. Electric actuators generate torque when the torque transmits to the output shaft, followed by transmission to the stem. The valve would then open or close when applying pressure to the stem.
Another consideration when choosing an electric valve is integration. Using an integrated electric valve actuator, operators can automate the system with programmable settings that activate during outages or other types of system failure or emergency situations.
If you have a multi-point positioning application, you'll likely want to use electric valve actuators because of their superior accuracy and repeatability.
How Do Pneumatic Actuators Work?
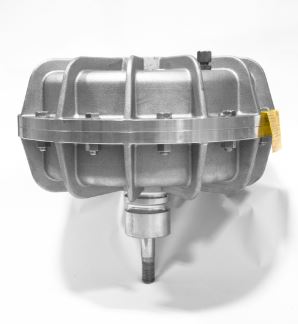
While electric actuators operate using electrical power, pneumatic actuators operate using compressed air. This air applies pressure to the diaphragm causing the valve stem to move up or down, which moves the valve plug to allow for the opening or closing of the valve to regulate flow.
Regulation of the airflow into the valves changes the pneumatic actuator's position, as the housing contains a diaphragm that pushes against the spring force. When removing air pressure, the spring force then moves the plug and stem back into their original positions.
How Do Pneumatic Valve Actuators Work?
Compressed air moves the diaphragm against or with the springs at different positions depending on whether you want to open or close the valve. Any change in air pressure will also cause the diaphragm to move against the valve plug or with the valve plug to open or close the valve.
You will need a pneumatic actuator that operates with enough air pressure to generate sufficient force which will help move the valve plug to the desired position. Another factor to consider is protection, as the actuator's housing should protect the valve and actuator from outside forces.
Additionally, the actuator should produce sufficient spring force and fluid power to hold the valve's plug in place. Fail positions will also allow for safer operation in the event of any type of system failure. E.g.: loss of air, loss of power, or diaphragm failure.
Consider the specific pressure levels required based on your operational needs. Depending on the size of the pneumatic actuator, air supply increases. Also, the process conditions play an important role in choosing the correct size actuator. Generally, larger diaphragm areas will allow for greater process pressure conditions, which leads to needing more force to operate the valve.
Also consider using a pneumatic actuator for hazardous environments or applications requiring simple end-to-end positioning.
Actuators from Baelz North America
Want more information on electric and pneumatic actuators to help you choose the right component for your needs? Download Baelz North America’s eBook, “Pneumatic vs. Electric Actuators: Choosing the Right One for Your Industrial Heating Process.” Alternatively, you can ask the Baelz experts directly. As a premier supplier of quality control components, including actuators, we can answer and address any questions or concerns you may have about these products.
Additionally, if you’re looking for a supplier for your next project, we’ve got you covered. We offer a broad selection of high-performance actuators to suit various customer applications. We provide professional project management to help you with all of your process needs. Contact us or request a quote to learn more.
To learn more about actuators offerings, check out our actuator product page or contact us today. For specific product questions or pricing details, request a quote.